45 South manages over 200 hectares of cherries within the heart of the renowned fruit growing area of Central Otago in New Zealand. Our ideal climate gives us a harvesting window of two months, starting with our early variety of Chelan, ripening in December – just in time for the festive holidays.
Our harvesting calendar then continues through numerous varieties, such as Kordia, Lapin, Sweetheart, Staccato, and finally Sentennial wrapping up the season in the early days of February. Over the years, we have migrated our growing systems from traditional style plantings to the dense and heavy cropping system called that of Upright Fruiting Offshoots (UFO), achieving an increase in yield, quality, and size.
We aim to have our product into the Asian and North American markets within 48 hours of the cherries being picked. To do this, we must always be looking forward into the future to observe any new technologies that may add value to the production chain, which in turn – improves the quality and consistency of our product that gets consumed and enjoyed all around the world.
The extremely perishable nature of cherries requires our production chain to be as efficient as possible. This includes the phase of transitioning the cherries from tree to cool storage as quickly as possible.
The introduction of Burro autonomous technology allowed us to tighten this transition even further, allowing our employees to work more efficiently at a faster pace, while also reducing the strain on the physically demanding tasks. Subsequently, this allowed us to achieve a reduced timestamp of our perishable goods being exposed to the sunny natural elements of mother nature and gave us the advantage of getting our product into the cool-chain environment faster.
The advanced AI software within the Burro units allows us to control the robot in numerous ways. From fully autonomous pre-programmed routes, to having the Burro accurately ‘follow’ an operator. Each method in controlling the robot suits a variety of different tasks appropriately.
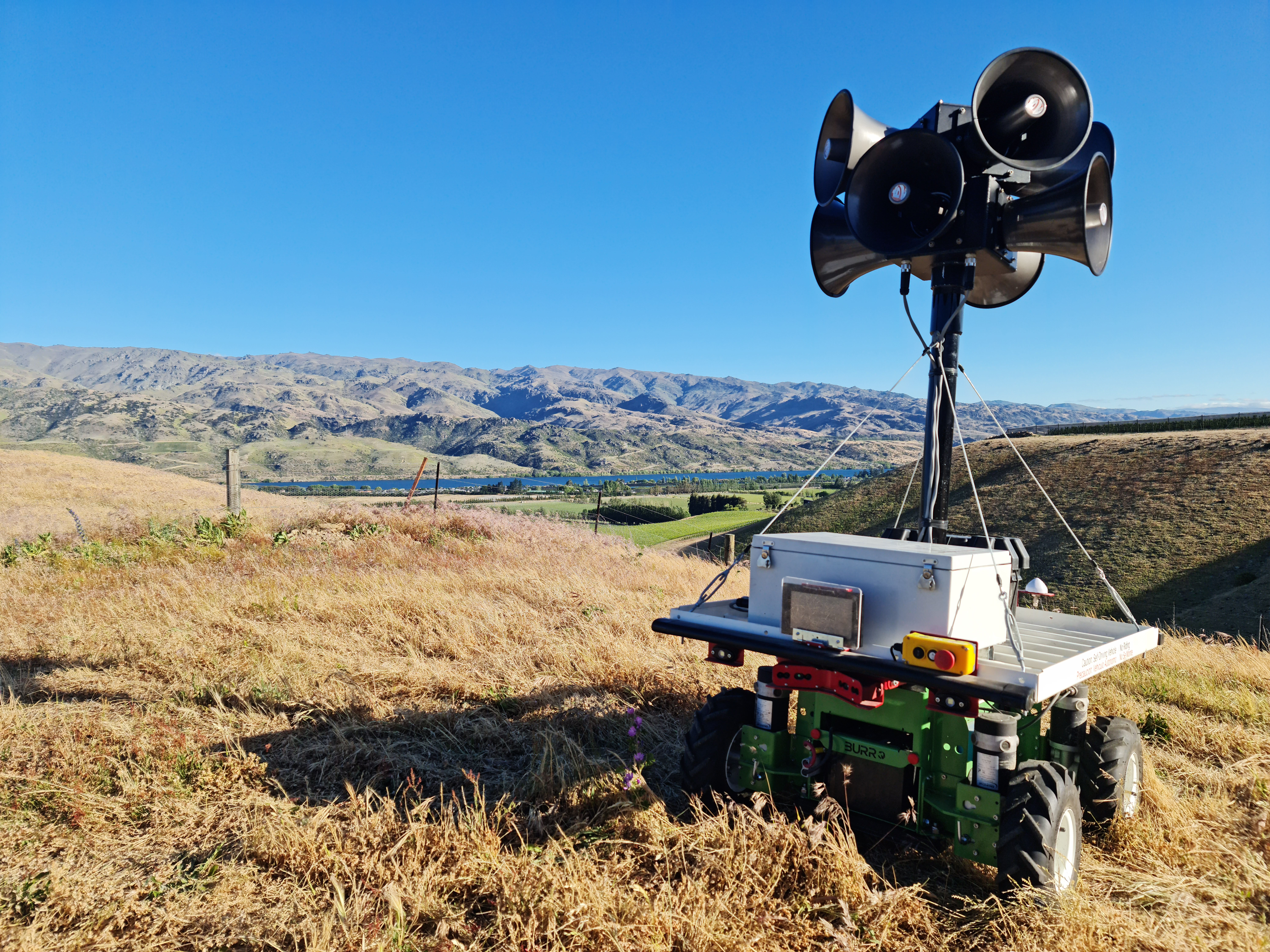
Our next step is fitting a mower unit onto the tail of the Burro, allowing us to mow and maintain our orchards rows with pre-programmed routes – removing the need for a tractor and utility operator.
Progression on sustainable orchard practices has also benefited greatly from introducing this technology. The Burro units are fully electrified, allowing us to greatly enhance our sustainable footprint in our operations, with estimated reduction in carbon emissions of up to 80,000kg’s of C02e annually, and 70% reduction in running costs per 40-hectare (100-acre) block of cherries.
As a company, if 45 South can continue to invest in technological advancements that adds value to our overall product and brand, we will continue to lead the market with our reputational quality. Small changes to the production chain, adds large changes to our product, people and planet. In addition to the above, please see below the details from us regarding the product and our company that supplied the machines to 45 South.
In the world of autonomous mobile robots for agriculture, the Burro stands out unique in that it’s actually being deployed commercially in a multitude of use cases globally when many other essentially similar products have failed to gain traction in the marketplace. We ask Chris Clifford of Agri Automation, distributor for Burro in New Zealand and Australia what is it about the Burro that makes the difference.
“In our view, Burro has succeeded in creating a machine that’s truly a multi-functional platform with the ability to carry loads, tow trailers, scout crops and work seamlessly with a range of add-on tools to mow, spray, deter pests etc and it’s this versatility that makes the Burro a viable addition to many operations".
"Furthermore, the Burro’s relatively small form factor and price point allows growers to operate a swarm approach with multiple machines rather than a single large expensive robot that has a limited range of functionality”.
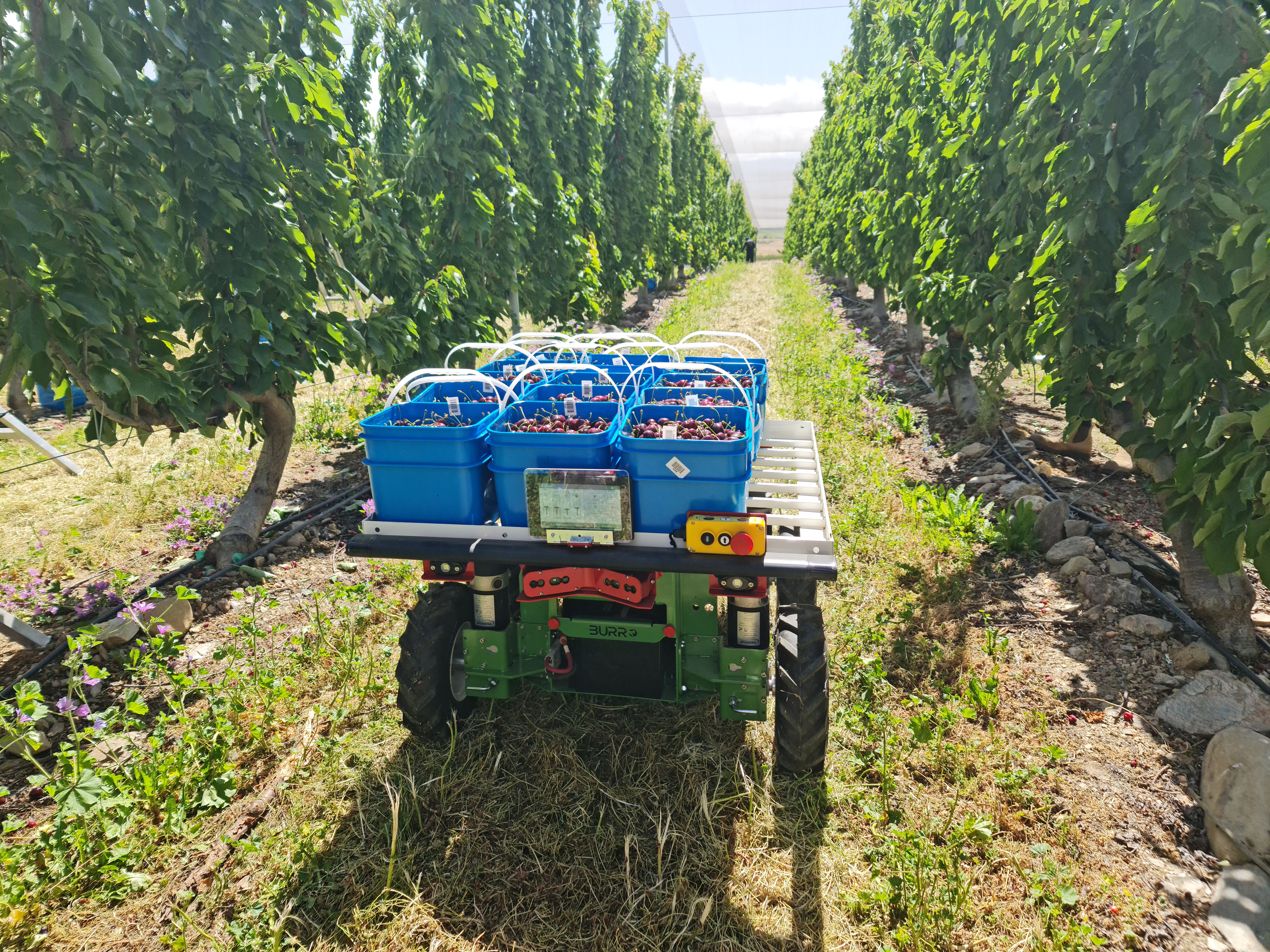
The Burro is simple to use and interact with and this makes integrating it into a commercial operation much easier. “You don’t need to have a degree in computer science or follow the Burro around with a laptop to keep it working” says Clifford.
The Burro has a range of operating modes that are simple to select and use even when wearing protective clothing. You have a manual mode that allows the Burro to be moved forward and backward or turned left and right. In ‘Follow mode’ the Burro’s cameras acquire the operator and lock onto them and as they walk away, Burro follows along, stopping, starting, and turning to maintain its place like a good dog.
Burro can also work in ‘Reverse follow mode’ where it will “walk away” from the operator at a controlled rate and recognise any sideways movement to steer the machine on its path. In ‘Row Navigation mode’ the Burro will use its Vision system and AI capabilities to navigate in a row of vines, trees or similar without the need for GPS.
In ‘Auto route mode’ the Burro can be “trained” to record a route that is required to be run multiple times, with the ability to name the route and upload it to the cloud platform for future use of for use with other Burros. This platform, known at Atlas, also allows for longer and more complex routes to be created and deployed to one or a multitude of Burros at any time.
Being 100% electric not only makes the Burro a sustainable choice to replace ICE powered motorbikes and small tractors, but the cost of operating is also vastly reduced. With the ability to run for approx. 25km on a battery charge (depending on the load) and to fully recharge in under 8-hours, the Burro can typically work a full shift without stopping.
Auto docking and charging stations are another recent release from Burro to enable the machine to dock and charge during pauses in its daily work program.
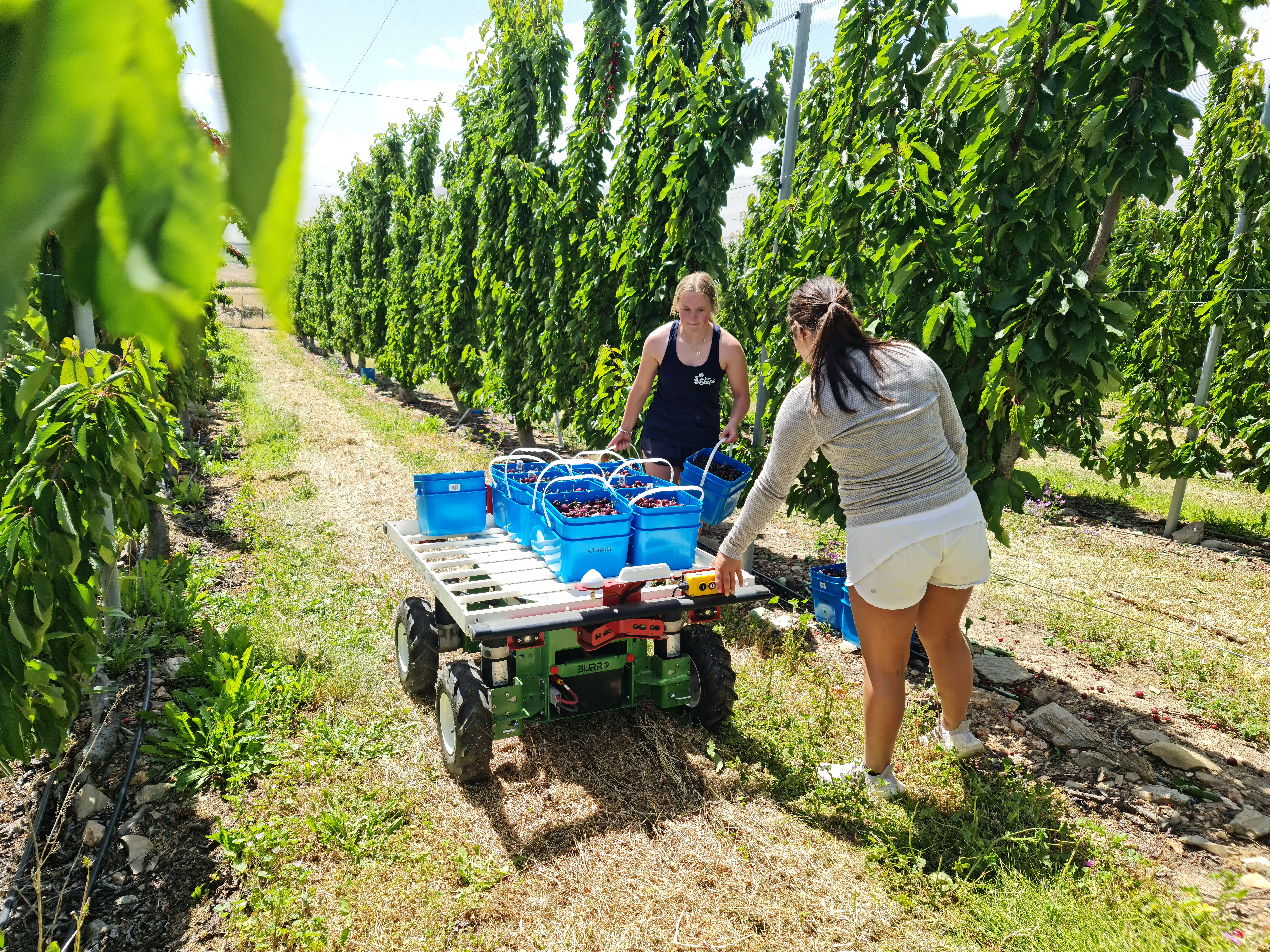
As with any autonomous machine, the question of safety is an important consideration. The Burro has four stereo cameras at the front and rear of the machine, giving it a wide field of view and the AI module processes data to identify obstacles and stop the machine when anything is in its travel path.
Once the obstacle clears, the Burro will automatically proceed on its path. As a secondary safety system, there are soft rubber bumpers across the full width of the machine, front and back and if these are pressed the Burro stop immediately, as it does if the red e-stop button located front and rear is pressed as well.
Standard on the new Grande model and optional on the smaller Burro is a LiDAR module that compliments the safety and navigational stack as well, especially when operating in an environment where GPS signal is denied or limited such as indoors.
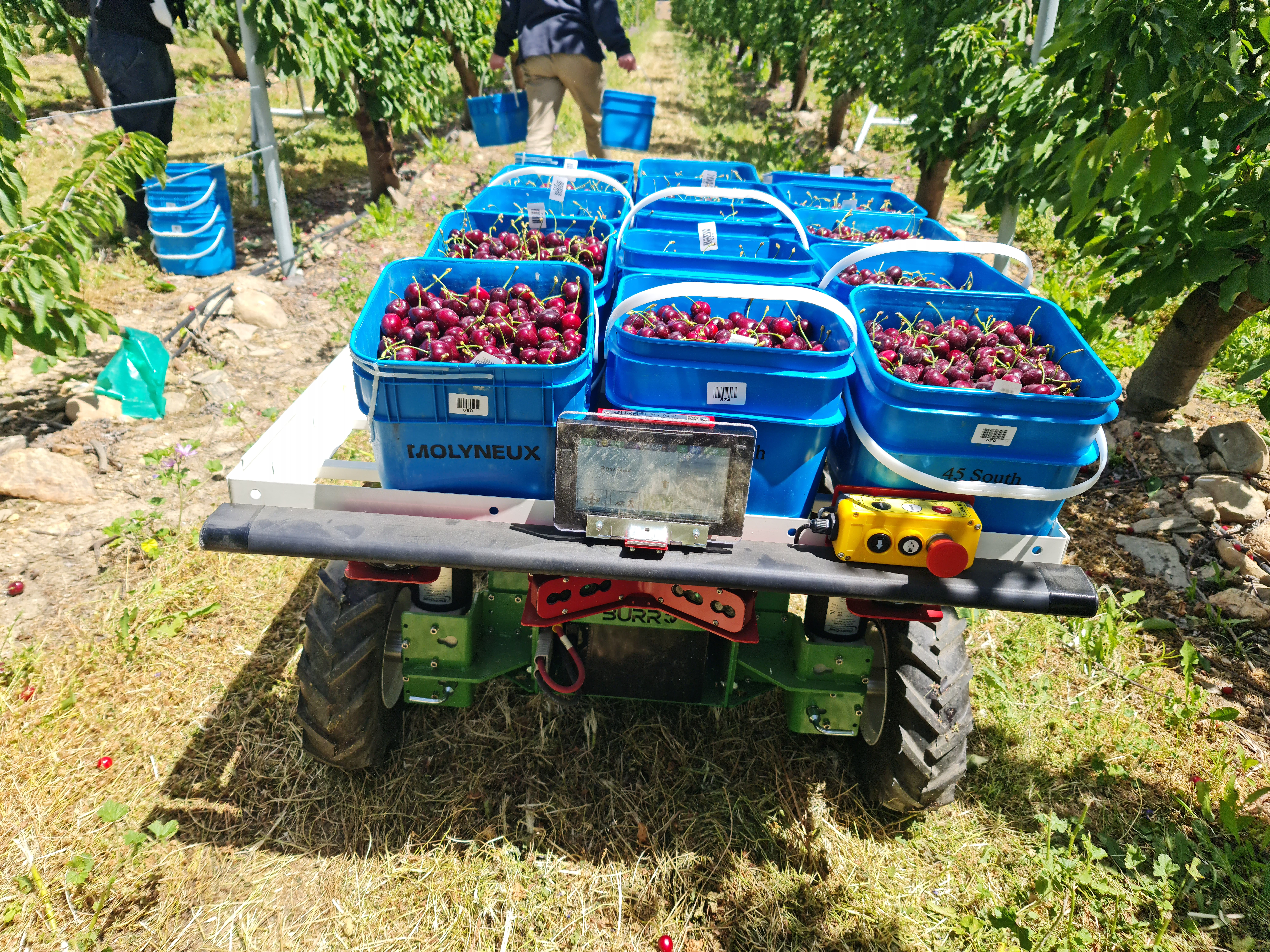
The standard Burro can carry 225kg on the tray and towing up to 700kg. Adding an XL kit increases the weight carrying capacity to 340kg. The new Grande model increases carrying capacity to a huge 700kg on a full pallet sized tray whilst being able to tow up to 2.25 tons. This huge towing capacity is proving very popular with large scale operations in industries such as nurseries that need to pull long trains of trailers around large sites.
Burro is designed to be simple and easy to operate right “out of the box” but customer support is an important factor in any successful deployment. With Burro’s online data dashboard displaying a wide range of operating data and system analysis as well as the 24-hour support from Burro technical and customer success teams, farmers can invest in the Burro robot with confidence that they won’t be left to figure it out alone.
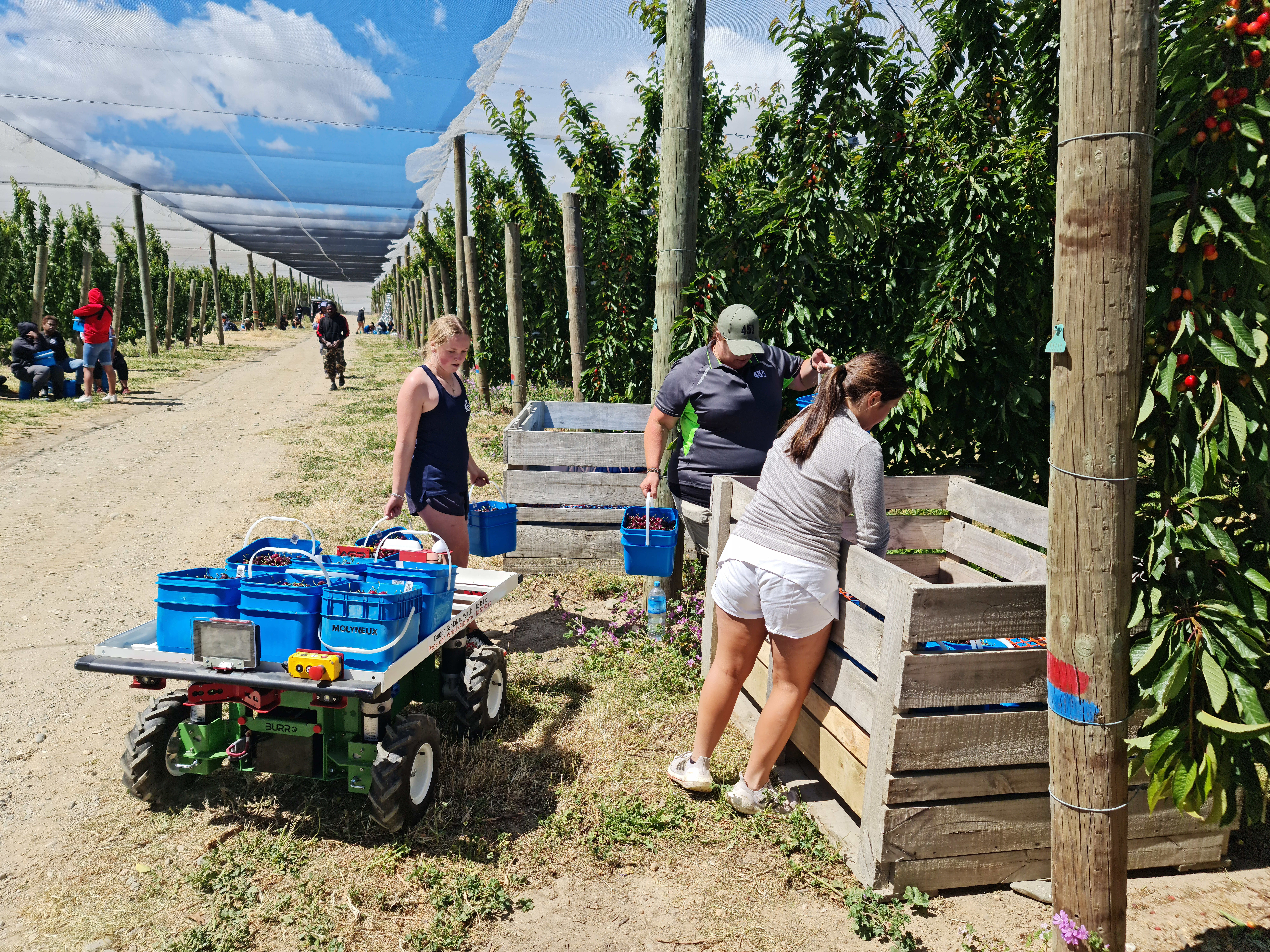
For Agri Automation, it is a pleasure to work with companies such as 45 South where the management have the vision to see the benefits to be gained from shifting from traditional labour-intensive practices to adopt and implement the Burros, firstly for harvest support and pest deterrence and then expanding into a range of further tasks including mowing and herbicide application.
“Watching the harvesting teams loading buckets of cherries onto the Burros to quickly get the fruit out of the row and into the chiller was very satisfying, especially when the traditional system saw the buckets being carried out by hand”.
Chris Clifford
Managing Director - Agri Automation
Images: Agri Automation
Cherry Times - All rights reserved