Changes in the cherries business are bringing new challenges as global demand is rising and exports are booming. Packhouses are under pressure to handle greater volumes and at the same time, they must also maintain or improve product quality. There are sensor based solutions that make this possible as Benedetta Ricci Iamino, Global Category Director for Cherries at TOMRA Food, explains.
Benedetta Ricci Iamino, Global Category Director per le ciliegie di TOMRA Food.
Even though cherries are pricier than other stone fruits, their sales are accelerating far more quickly. Global demand is rising, exports are booming, and new growers and packers are entering the market to profit from these opportunities.
The popularity of cherries is especially evident in their biggest market, China, during the nation’s New Year: to satisfy a seasonal feeding frenzy, packhouses have to work around the clock, while exporters rush the produce to market in ‘express’ boats and aircraft.
This is emblematic of what’s happening throughout the year and around much of the world: these little red treasures simply can’t be grown or packed fast enough.
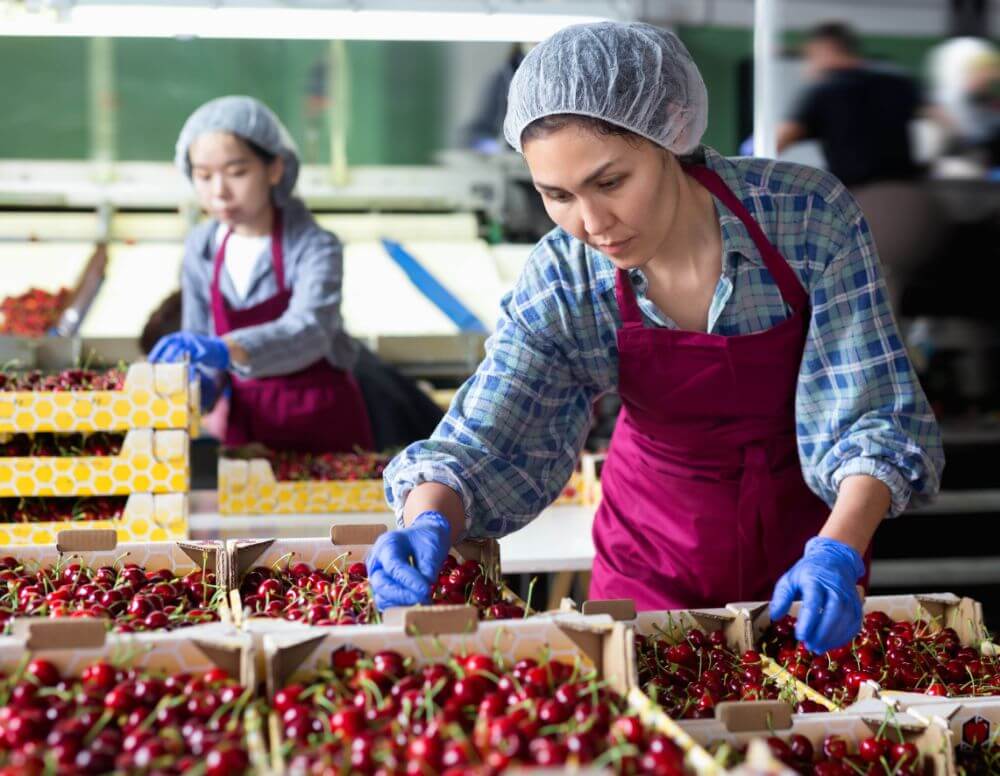
There’s no end in sight to the growth in demand for cherries. In developed nations, there’s an increasing appetite for cherries for their natural healthiness. In developing nations, the growth in middle-income households is fuelling demand.
And in almost all markets, cherries are increasingly wanted not only for consumption at home but also as an ingredient for commercial bakery products. Market researchers forecast that the global cherry market will continue to expand over the next five years at a compound annual growth rate of anything from 5% to 10%.
In the race to keep up with demand, the world’s biggest cherry grower, Türkiye, increased production four-fold in little more than a decade. The United States remains firmly established as the second-biggest grower, but third- and fourth-placed Russia and Iran are being caught by Uzbekistan and Chile. The latter recently doubled production in just three years.
Big production increases are also being made in Tajikistan and Kyrgyzstan, where the Central Asian climate is well-suited to cherries, and where it is relatively easy to access the huge Chinese market.
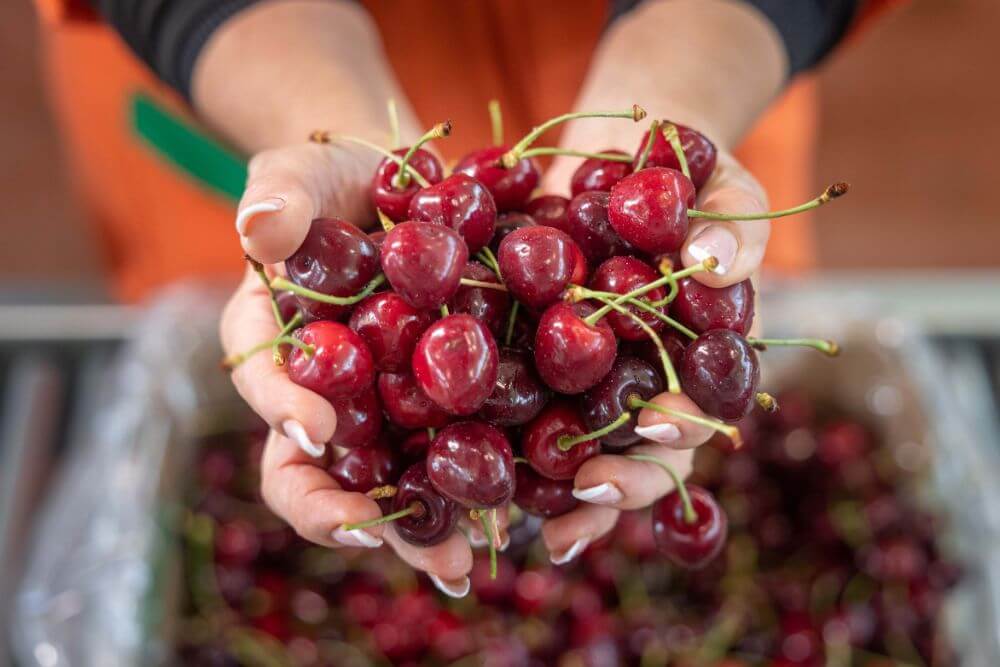
In all of these territories and many others, packhouses are constantly under pressure to handle greater volumes. At the same time as increasing throughputs, they must also maintain or improve product quality. Consumers buy with their eyes, expecting cherries to have a consistent color; skins that are smooth, firm, and free from pitting; and long green stems indicative of freshness.
For packhouses, this is a challenge, because cherries are notoriously vulnerable to handling damage and exceptionally difficult to sort and grade. Careless packaging can bruise or cut the fruit and loosen or remove stems. But to reliably detect defects, it is necessary to inspect each piece of fruit in its entirety, through 360 degrees, something many packhouses have traditionally found impossible.
Understanding the challenges
It is now possible, however, to achieve a complete 360-degree inspection of the fruit, thanks to state-of-the-art sorting and grading technologies. This technology also increases output, improves product quality, reduces the problems associated with recruiting and retaining labor, reduces food waste, and maximizes pack out.
Dynamic Lane Balancer - Tomra
One of the leading manufacturers of integrated post-harvest-to-pack solutions for cherries is TOMRA Food. Long renowned for setting the benchmark in optical sorting and grading technologies for the food industry, TOMRA broadened its offering to include solutions for cherry packhouses (and lines handling blueberries and other small fruits) by acquiring two innovative New Zealand-based companies, BBC Technologies and Compac.
Today all the solutions originated by those two companies – as well as solutions introduced since their acquisitions – are manufactured, sold, serviced, and supported directly by TOMRA. This means cherry packhouses now benefit from TOMRA’s world-class technical expertise and global presence. The company operates in the United States, Europe, South America, Asia, Africa, and Australasia.
Building on this international reach, TOMRA has taken measures in the last year to strengthen customer support and speed of response in cherry-growing regions. This included sending a team of experts to all major cherry regions around the world, to work closely with packhouses and share in experiencing their challenges. This detailed knowledge will help inform the refinement of TOMRA’s existing solutions and inspire the design and development of new ones. TOMRA’s mission with cherries, as with other food categories, is to lead the resource revolution in a world where every piece of food counts.
Separating, sorting, and grading
TOMRA’s cherry solutions are already unrivaled for their effectiveness in performing every important task on the line: infeed, sorting, grading, filling, packing, and product traceability. These solutions are unmatched in their throughput capabilities, handling gentleness, grading accuracy, and packing speed. And because they are modular and scalable, they can be tailored to businesses of all sizes.
As the cherries arrive at the packhouse, TOMRA’s solutions start with infeed front-of-line loading systems.
Cascade singulator - Tomra
Then the company’s revolutionary Cascade Singulator separates cherry clusters with a gentle carrying method and superior cluster separation. Whereas traditional cluster cutters push cherries at speed to blades, putting the fruit at risk of pitting and bruising, the Cascade Singulator reduces the cherries’ velocity by using a non-motorized water system that decelerates the water flow between each bank of separation.
By improving separation location, at the knuckle where two cherries join, the cluster’s center is aligned to achieve clean and even separation without the risk of tearing the cherries. This also reduces maintenance costs and the operational hours usually needed by other systems for cleaning and adjusting the machine.
To optimize capacity when filling each lane, TOMRA’s unique dynamic lane balancing technology allows up to 10-15% more capacity (number of fruits) per lane than other systems. Next, the cherries move along the line for sorting and grading. TOMRA offers the Small Fruit Sorter (SFS) with InVision2 and TotalView Plus to accept, reject, or redirect the fruit for sale at a lower grade according to a wide range of criteria.
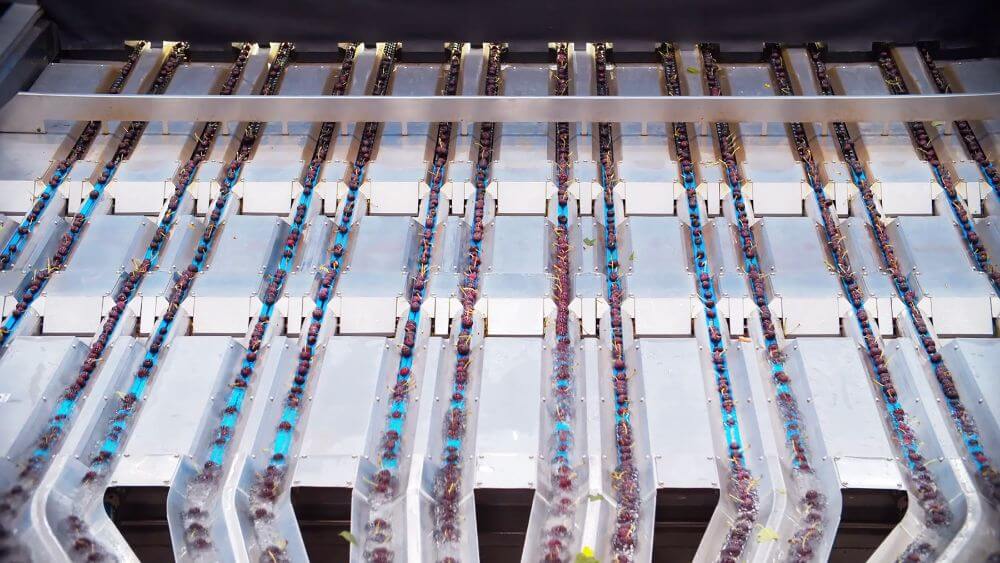
InVision2 with TotalView Plus is the only available inspection technology capable of viewing 100% of the fruit without blind spots and at full production speeds. Compared to other sorters, TotalView's end-view cameras are located at lower inspection angles and closer to the fruit. Superior image quality improves the identification of nose cracks, stem bowl mildew, and suture splits. Additionally, the Small Fruit Sorter is gentler on the cherries than any other available technology available in the market, using a series of patented systems that transport the cherries in water all the way to the camera for inspection.
Using TOMRA sorters results in superior size-grading accuracy for increased packout of premium packs; reduced giveaway; and greater sizing homogeneity. Efficiencies and packout returns are also enhanced by the rejected fruit having an exceptionally low good-in-bad ratio, typically as little as 2-4%.
Further efficiency gains are made through TOMRA’s point-and-click defect classification, which allows defects to be classified and product grades assigned according to customers’ tolerances. By mixing-in allowable defects, food waste is minimized and the value of each piece of fruit maximized. Defect classification also makes it possible to see packout by grade, to see which defects are resulting in the grades, and to provide feedback to suppliers to help improve future orchard management.
Filling and packing
Now the cherries are nearing at the end of the line, where they are handled gently by TOMRA’s filling machines. These automated solutions can simultaneously pack different grades of fruit for different markets. The CURO filling system – available with 2, 8, 12, and 16 filling stations – delivers consistent, high-speed filling at precise weights, with the flexibility to easily switch between a wide range of packing options. TOMRA offers several different types of box filler to ensure accurate, high-volume filling and to accommodate a variety of box sizes and weights.
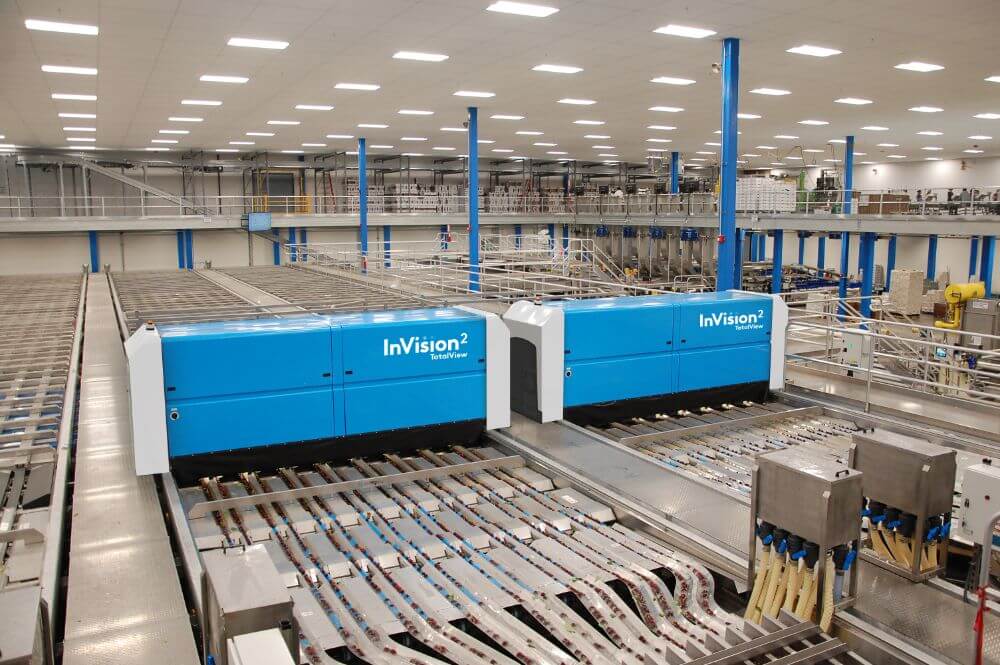
From one end of the pack line to the other, all these components are linked to communicate with each other to form an integrated solution. And a quality tracking system can keep tabs on the whole process, from harvesting to processing, packing, and point-of-sale.
Named Freshtracker, this system’s software allows packhouses to trace the origins and characteristics of individual products. It also lets packhouses know when one grower’s product has been packed and another’s is rolling down the line, so that there’s no need for a break in production between the two. Freshtracker can also compare and analyze yields to ensure a high-quality end product and manage production efficiently.
CURO - Tomra
This, like so many other automated line solutions, contributes to reducing food waste and increasing profit. When packhouses decide to invest in such solutions, they quickly find it’s a wise move. And when the provider of those solutions is TOMRA - which combines global R&D power with a local presence and customer-centric mindset - packhouses can rest assured they will receive the operational training and technical support to ensure these machines achieve optimum performance with minimum downtime.
Contact Tomra:
Web Email
Cherry Times - All rights reserved